Les traitements de surface pour les ressorts sur mesure
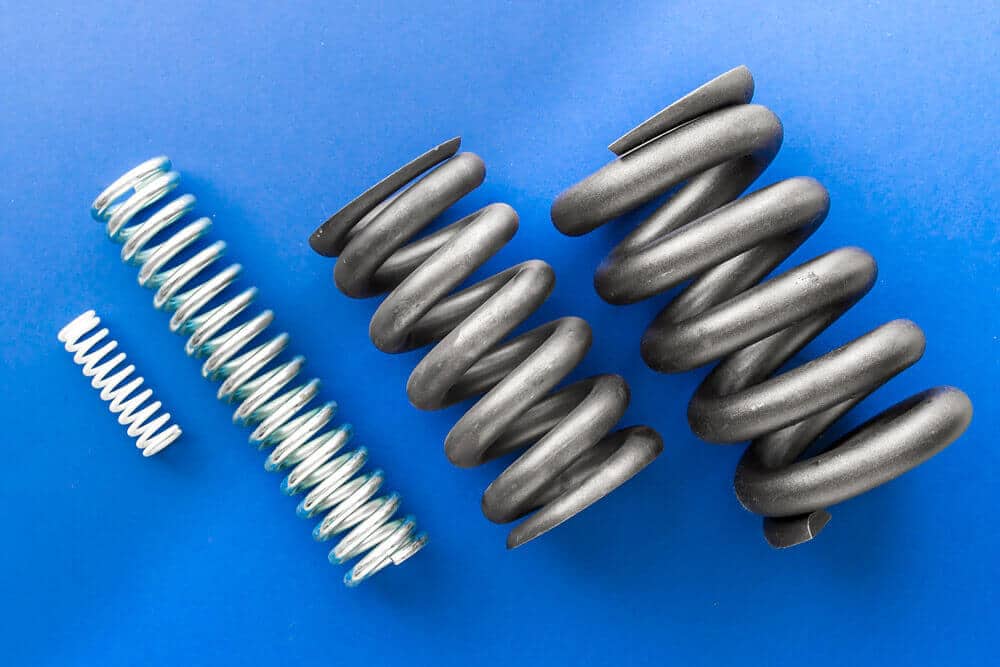
Les traitements de surface pour les ressorts ont pour objectifs principaux de modifier leurs propriétés. Comme améliorer la résistance à la corrosion simple ou sous contraintes, améliorer la résistance à la fatigue, améliorer la résistance à l’usure et/ou améliorer l’aspect esthétique. Les fabricants de ressorts sur mesure ne réalisent presque jamais le traitement de surface eux même. C’est un travail de spécialiste avec une réglementation très stricte aux vues des risques que cela engendre. Nous allons alors décrypter les différentes caractéristiques des traitements de surface utilisés dans le domaine du ressort.
Il faut savoir que chaque traitement de surface est soumis au test Brouillard Salin (BS), qui permet d’évaluer la résistance à la corrosion. Ce test nous donne une idée du nombre d’heures que peut résister la pièce avec traitements de surface dans un environnement humide et salé avant corrosion. Il y a alors deux types de corrosion, la rouille blanche qui apparaît lorsque le traitement de surface est attaqué et la rouille rouge quand c’est le métal de la pièce qui commence à être attaqué.
Les principaux traitements de surface utilisés pour les ressorts sur mesure
Le zingage est le traitement de surface le plus utilisé sur les ressorts sur mesure. Il englobe tous les traitements de surface qui entraînent la formation de zinc recouvrant la pièce pour la protéger (Souvent entre 5 et 15 µm). Le zinc étant très réducteur, il empêche la dégradation du métal qu’il protège car il est oxydé à sa place (corrosion du revêtement anodique = le métal protecteur est moins noble que le métal protégé, seul le métal anodique est attaqué). Appliqué principalement à l’acier par dépôts électrolytiques, il a pour effet de lutter contre la corrosion.
Il existe plusieurs types de zingage : Le zingage bichromaté qui est à base de chrome 6. Historiquement le plus utilisé mais qui a fait scandale en Amérique pour ses propriétés cancérigène. Nous trouvons également le zingage à base de chrome 3. Le zingage noir avec fixateur (46 heures tenue BS), le zingage blanc qui est le plus utilisé (120 heures tenue BS), le zingage irisé (200 heures tenue BS). Par-dessus, nous pouvons rajouter un Top Coat qui permet d’éviter les frottements ainsi que d’augmenter la tenue BS.
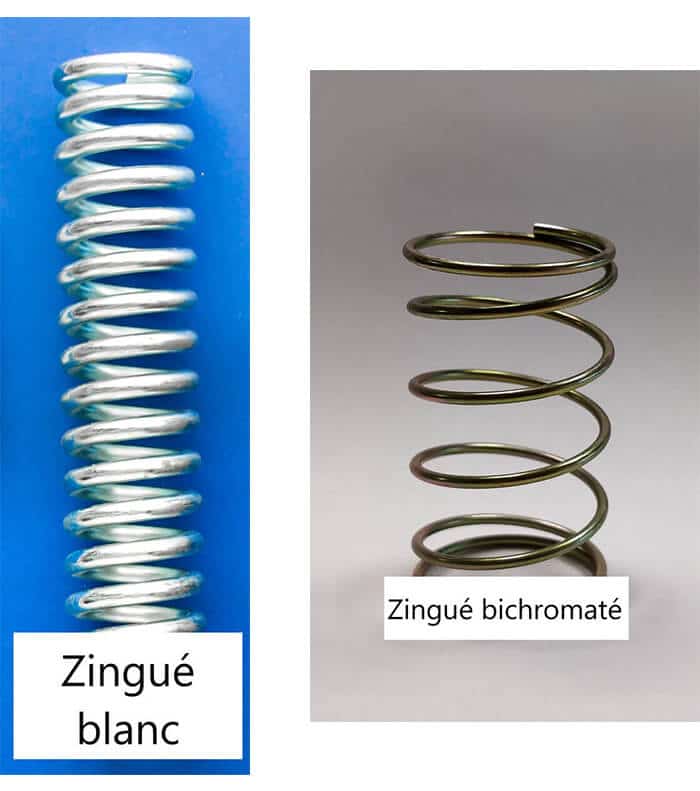
Il est aussi parfois possible que le fil soit zingué pré-galvanisé. La galvanisation est le fait de recouvrir une pièce de zinc pour éviter la corrosion. Ce terme désigne essentiellement le procédé de « galvanisation à chaud trempé ». Le principe est de plonger la pièce dans un bain de zinc en fusion à 450° C. Ce qui fait une différence avec le zingage classique qui lui est un bain avec des ions de zinc qui viennent s’accrocher à la pièce.
Un autre type de zingage, c’est le zingage lamellaire. Il procure au ressort une haute résistance à la corrosion. Il est chargé en zinc et en aluminium. La méthode utilisée pour le zingage lamellaire est la centrifugation ou la pulvérisation. L’application se fait de plusieurs couches de base (Base Coat) et une couche de finition si besoins (Top Coat). Cette couche de finition permet un meilleur coefficient aux frottements et améliore la tenue à la corrosion. De plus ce procédé ne fragilise par la pièce car il n’est ni par dépôt électrolytique, ni avec de l’acide.
Aussi utilisé dans le monde du ressort, le polissage électrolytique ou électro polissage. Principalement pour l’inox, la procédure consiste à enlever de la matière. La pièce est plongée dans un bain d’acide fortement concentré (électrolytique) où l’on applique un courant électrique. En fonction de l’intensité du courant à travers la surface, le processus d’électrochimie produit une dissolution plus ou moins importante. Ce traitement de surface a pour avantages, l’éliminations des impuretés, la résistance à la corrosion plus élevée, empêche l’adhésion de dépôt et supprime la couche de BELIBY (rugosité due aux stries d’usinage). En revanche lors de cette opération, il faut prévoir une perte d’épaisseur, généralement entre 5 et 10 µm. Il est possible de retirer des épaisseurs plus importantes allant jusqu’à 50 µm. Le processus est compliqué à mettre en place pour régler le niveau de l’intensité du courant, la température du bain et la durée du traitement.
Les traitements de surface « physique »
En ce qui concerne les traitements de surface physique, il y a la tribofinition. Aussi bien utilisée pour l’acier que pour l’inox, le principe est de nettoyer la pièce pour ôter la couche de calamine grâce à un mélange d’abrasifs. Ce procédé est utilisé pour des pièces nécessitant une propreté parfaite. La pièce est mise dans un mélange d’abrasif nommé « média », ressemblant à des petites pierres. Ce mélange est ensuite mis en mouvement vibratoire, oscillatoire ou rotatif dans une cuve ouverte ou fermée. Le résultat obtenu est dû aux frottements entre le mélange et la pièce. Il dépend également du type d’équipement utilisé, de la composition du mélange, de la vitesse et la durée de l’opération.
Le deuxième traitement de surface physique utilisé pour les ressorts est le grenaillage de précontrainte. Il permet d’augmenter la durée de vie dynamique. En effet, le grenaillage offre au ressort une meilleure résistance à la fatigue. Cette opération mécanique vise à déformer plastiquement le matériau dans une couche superficielle en le martelant avec des billes de métal projetées à grande vitesse. Pour que le grenaillage soit efficace, il faut qu’il soit régulier car le ressort casse toujours dans la zone la plus faible. Plusieurs critères rentrent en compte pour le grenaillage, l’angle de frappe (en général 85°), la vitesse du média, sa taille, la quantité de billes expulsée… De plus, cette opération ne peut être effectuée seulement sur les ressorts dont l’espace entre les spires est suffisant pour laisser passer les billes.
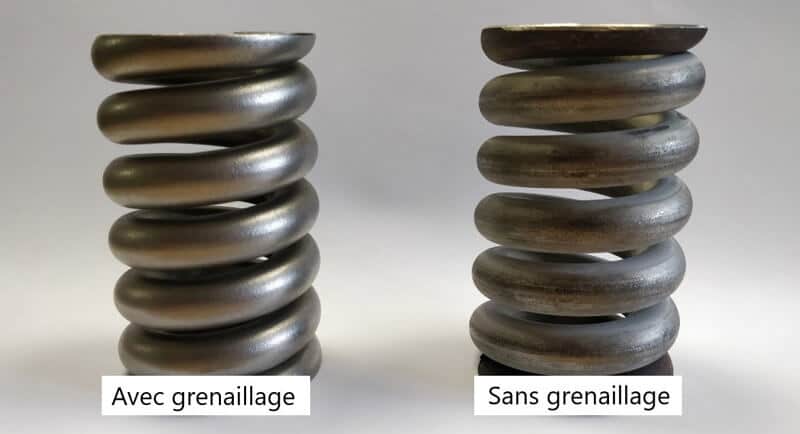
Les traitements de surface « chimique »
Pour les ressorts il existe aussi des traitements de surface par dépôts chimiques. Il y en a plusieurs mais ne sont pas forcément souvent utilisés. Prenons d’abord les plus utilisés. La passivation, souvent utilisée pour l’inox. Il s’agit de traiter le métal avec des acides pour éliminer le fer libre de la surface puis recouvrir la pièce d’une couche protectrice d’oxyde de chrome qui empêche la corrosion. Cette couche protectrice doit être régulière sur la pièce pour éviter les dommages. Elle est réalisée en milieu acide (acide nitrique), par immersion en bain ou par pulvérisation. La quantité d’acide utilisée, la température et la durée du processus de passivation dépendent du type d’alliage. En ce qui concerne la tenue BS, cela va varier selon la couche de passivation posé sur le ressort.
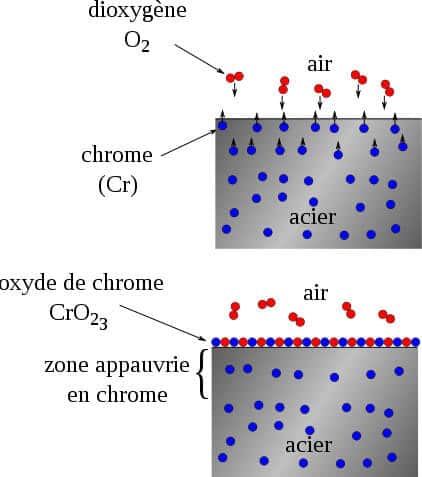
Lorsque l’on parle de traitement de surface pour les ressorts, c’est le zingage qui est le plus utilisé comme nous l’avons vu un peu plus tôt. Cependant, on retrouve un traitement de surface qui se rapproche du zingage, c’est le nickelage. L’alliage nickel/phosphore est obtenu par la réduction catalytique d’un sel de nickel. Ce traitement est suivi d’un dégazage.
Le dégazage est un principe qui vise la déshydrogénation d’une pièce ayant été abîmée par l’hydrogène. Souvent appliqué aux pièces qui subissent un traitement électrolytique, il doit être effectué dans les 4 heures après l’application du traitement de surface et de préférence dans l’heure qui suit.
Suivant les applications de la pièce, des traitements thermiques peuvent durcir la couche (de 600 à plus de 850 HV). D’aspect brillant, la pièce ne nécessite pas de polissage après le nickelage, il est donc souvent utilisé pour l’esthétique. Utilisé principalement sur l’acier, n’oublions pas qu’il offre également une protection contre la corrosion et de bonnes propriétés de glissements.
Il existe 3 types de nickel (sans traitement thermique) :
- Bas phosphore (1 à 4%) : a une forte dureté en sortie de bain (700 à750 HV). Tenue au Brouillard Salin de 200 heures.
- Moyen phosphore (5 à 9%) : offre une meilleure résistance à l’usure et de l’homogénéité, de l’épaisseur mais est moins dur (500 à 550 HV). Tenue au Brouillard Salin de 200 heures.
- Haut phosphore (≥10%) : offre une résistance élevée à la corrosion, c’est un compromis entre les deux types précédents (500 à 550HV). Tenue au Brouillard Salin jusqu’à 1000 heures.
Avant le dépôt de nickel, une préparation de surface doit effectuée, c’est le dégraissage et le décapage, puis rincée après. C’est une opération qui est vrai pour tous les traitements de surface
Voyons maintenant le chromage, qui consiste à un dépôt électrolytique de chrome. Nous distinguons 2 types de chromage. Le chromage décoratif, qui permet de fournir à la pièce un aspect brillant durable et le chromage dur dont la principale fonction est de lutter contre la corrosion (revêtement cathodique). La résistance à la corrosion est nulle si le dépôt est endommagé. Le chromage dur a aussi comme propriétés, la résistance à l’environnement ou les frottements sont sévères, ainsi qu’une bonne tenue en fatigue et à la résistance thermique. Souvent utilisé pour l’acier, le chromage peut être réalisé sous vide, mais la technique la plus prometteuse est la Pulvérisation Cathodique Magnéton (PCM). Un grenaillage de précontrainte peut également être réalisé avant le chromage.
Dans la même famille que le chrome, nous retrouvons l’achrolyte. Très similaire dans la mesure où le résultat est extérieurement indiscernable. C’est un procédé électrochimique avec un alliage composé d’étain et de cobalt. Il est souvent utilisé en substitue du chromage lorsque ce dernier n’est pas possible pour des petites pièces en masse ou lorsqu’il est excessivement coûteux.
Poursuivons maintenant avec les traitements de surface que l’on utilise très peu dans le monde du ressort. Tout d’abord le doré, surtout utilisé pour sa conductibilité, il empêche également trop d’étincelles lors de la mise en marche. Il est cependant peu résistant au niveau mécanique et chimique. La shéradisation est un traitement de surface très peu utilisée qui consiste à obtenir un revêtement par procédé thermochimique de diffusion de zinc. La pièce est chauffée à 400° C en présence de poussière de zinc et de matériau inerte tel que le sable. Ce traitement de surface peut atteindre 400 heures en tenue BS.
Nous avons aussi la phosphatation, qui est un traitement réalisé par immersion dans un bain d’acide. Quand il s’agit d’améliorer les propriétés de frottement la phosphatation sera au manganèse pur et au fer/manganèse. Pour améliorer sa résistance à la corrosion la phosphatation sera au zinc pur, au zinc/fer et au zinc/calcium. On parle de phosphatation grasse lorsqu’elle est suivie d’une lubrification. En plus de cela la phosphatation permet l’augmentation de la dureté de surface. En ce qui concerne la tenue BS elle est de 2 heures sans finition grasse et de 96 heures avant rouille rouge avec finition grasse.
Les traitements de surface « peinture »
Pour les traitements de surface peinture, il y en a 2 types. La cataphorèse, dont le principe est d’immerger la pièce dans un bain de peinture hydrosoluble. Le but est ensuite de faire migrer les particules de peinture vers la pièce au moyen d’un courant électrique de l’anode vers la cathode. Les particules se déposent alors uniformément sur la pièce immergée.
La deuxième technique que nous pouvons trouver est la peinture électrostatique. Elle confère aux pièces une résistance à la corrosion dans le temps ainsi qu’aux variations de température. De plus, elle procure un esthétique parfait. L’objectif est que la peinture soit attirée sur le métal grâce à un courant électrique qui traverse la pièce. La peinture électrostatique assure une longévité de la pièce dans le temps car elle lui procure un faible taux d’usure. Il peut y être appliqué de la peinture liquide un peu moins utilisée car il arrive qu’elle coule. Le plus utilisé aujourd’hui est la peinture en poudre qui vient fournir une pose parfaite.
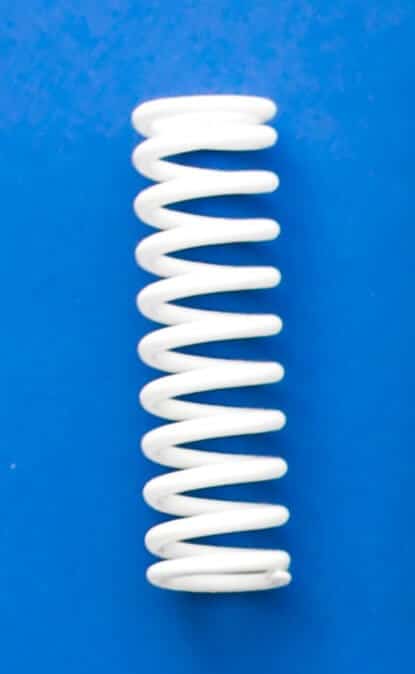
Le dernier que nous allons aborder, n’est pas une peinture mais un huilage. Ce traitement de surface propose à la pièce de très bonnes propriétés de glissement ainsi qu’une réduction des frottements. L’huilage est donc un recouvrement de la pièce par immersion dans un bain d’huile.
En conclusion le traitement de surface appliqué dépend fortement de l’utilisation de la pièce. Il n’y a pas de traitements de surface parfait, chacun a ses caractéristiques. Il est donc important de les connaitre et de voir quel est celui qui correspond le mieux aux contraintes qu’offre l’environnement dans lequel évolue le ressort. Evidemment il en existe beaucoup d’autres mais nous avons fait une sélection des plus courant traitements de surface appliqué aux ressorts.
Sources
- https://www.tegma.fr/traitements/traitement-surface-sherardisation/
- https://www.cetim-certec.com/wp-content/uploads/2017/04/traitement-de-surface-des-aciers.pdf
- Wikipédia
- https://www.a3ts.org/association-a3ts/traitements-thermiques/traitement-surface/
- https://www.worldstainless.org/Files/issf/non-image-files/PDF/Euro_Inox/Electropolishing_FR.pdf
- https://www.bst-traitement.fr/zingage-electrolytique/
- https://www.delcros.fr/passivation-inox
- https://www.wattco.com/fr/casestudy/quest-ce-que-la-passivation-pourquoi-avons-nous-besoin-de-passiver-les-thermoplongeurs-a-bride/
- https://www.verbrugge.fr/nickelage-chimique/
- http://www.kerbirio.fr/huilage/
- https://www.techniques-ingenieur.fr/base-documentaire/materiaux-th11/traitements-de-surface-des-metaux-en-milieu-aqueux-42359210/chromage-m1615/
- http://www.mecaweb.info/ANGERS-NICKEL-CHROME.aspx
- https://www.chemie.de/lexikon/Achrolyte.html
- https://www.a3ts.org/actualite/commissions-techniques/fiches-techniques-traitement-surface/phosphatation-manganese-sur-acier/
- http://www.kerbirio.fr/degazage/