Spring materials: Overview of standard EN 10270
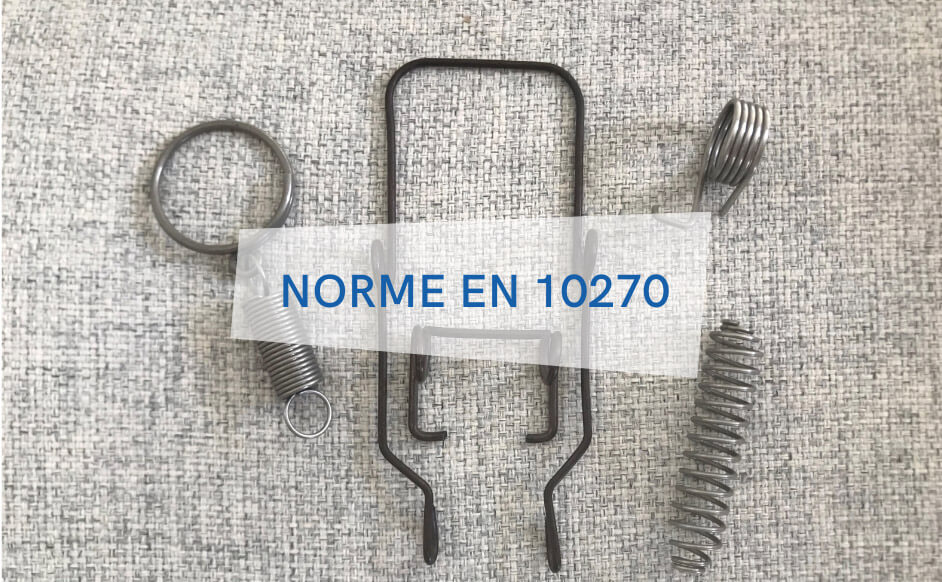
What is the purpose of a spring? Start this article with a question is not common. However, this is the first thing to do when it comes to spring materials. It can be defined as a system whose function is to deform under action of a force (or a torque) and then to restore the stored energy when it returns to its initial form.
Whether it’s custom made or not, whether it’s small, large, tensile, compressive, twist, etc., the goal will always be the same. The choices of possible materials are rather vast but there are few things to know about this.
Characteristics of spring materials for a good design
To be effective, the spring materials must have elastic properties which will allow the part to produce movement without failing. All so-called “spring” materials do not necessarily have the same elasticity. This property allows the part not to undergo plastic deformation under low stress.
The material must also resist to applied stresses. When the spring works statically, it must not be plastically deformed, therefore it must work only in the elastic domain. On the other hand when the spring works in dynamics, it must resist the cyclic forces. In conclusion, the material must be compatible with the working frequencies envisaged. Several factors must be considered, in particular related to intrinsic properties (production structure, etc.) and extrinsic properties such as surface condition.
The third characteristic often considered when choosing the material is its resistance to salt spray corrosion test. The work environment of a spring can be hostile, or quite simply very demanding (high health issues for example). Depending on the level of requirement, or economic models, the use of a surface treatment can be invaluable.
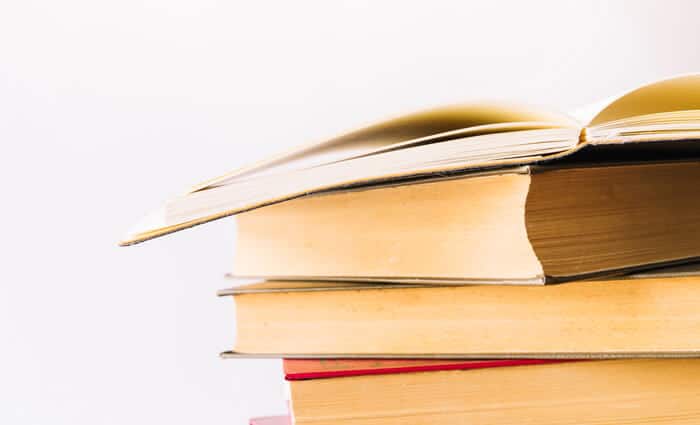
Finally, we can also talk more generally about the work environment expected of a spring. Indeed, let us note for example that the ambient temperature a spring will have to work is essential. The materials are designed to work in wide temperature ranges.
Also, some designers define their springs so that fulfills several functions. It should be noted here that certain materials having interesting elastic properties are also good electrical conductors. These materials will not be covered in this article.
Understanding all these parameters is essential from the design stage. Otherwise, it can directly be one if not THE cause of failure. Note that raw steel or Galva and stainless steel springs fulfill many of these points, for fairly reasonable price levels. Therefore they are often privileged.
Unalloyed, cold drawn and patented steels (EN 10270-1)
The first family of steels in the EN 10270 standard that we will see is unalloyed, cold drawn and patented steel. During wire drawing, the material undergoes strain hardening which increases its mechanical strength.
Patenting is a heat treatment that aims to create or recreate a pearlitic structure. This allows a better aptitude for cold deformation and therefore for cold drawing.
For this category of steel, the materials are divided into 5 classes :
- SL = Low resistance to static regime. Applied to compression, tension or torsion springs subjected to low static tension. This steel has low mechanical strength.
- SM = Average resistance at a static regime. Applied to compression, tension or torsion springs subjected to a medium static tension or which can be brought to work rarely in dynamics. This steel has an average mechanical resistance.
- SH = High resistance to a static regime with high mechanical resistance. Applied to compression, tension or torsion springs subjected to high static tension.
The so-called “S” steels are mainly intended for static loads.
- DM = Average resistance at dynamic speed. Applied to compression, tension or torsion springs subjected to medium to high dynamic stresses.
- DH = High resistance to a dynamic regime. Applied to compression, tension or torsion springs subjected to high static tension or to medium dynamic work.
It seems that currently only DM and DH yarns are patented. The SL, SM and SH wires would be raw from Stelmor hot drawn and cooled. This means that it is a continuous cooling of the wire rod.
The difference between so-called “S” and “D” steels is linked to a better guaranteed surface quality. Particularly in relation to the size of the defects and limited or even prohibited decarburization thickness for “D” steels.
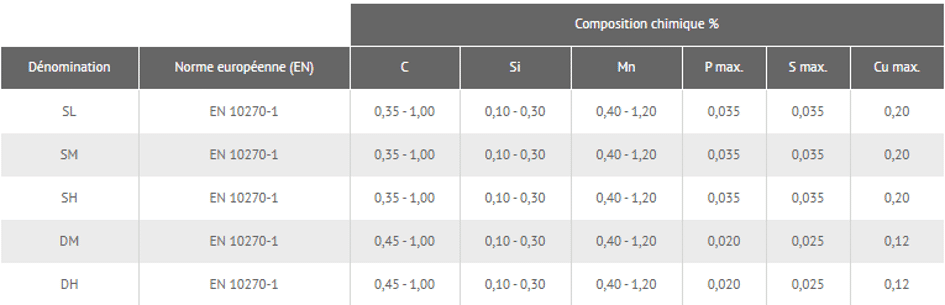
A spring made with a material of this family can work at very low temperatures but undergoes relaxation at high temperature. It is considered to be at full capacity between -80 ° and + 150 ° C.
Oil hardened and tempered steels (EN 10270-2)
The second steel is oil hardened and tempered steel. Called EN 10270-2, this steel is rather similar to EN 10270-1 steel, except that it is quenched. In fact, EN 10270-1 steels are hardened by strain-hardening while EN 10270-2 steels are hardened by quenching. This hardening allows the steel to have better mechanical resistance. Also, this material has very few impurities.
Here again there are several classes of steel EN 10270-2, we can count 3 of them:
- FD (FederstahlDrähte): Drawn steel for springs.
- VD (VentilferstahlDrähte): Steel wire for valve springs.
- TD (TransmissionDräthe): Steel wire for clutch springs.
VD and TD wires are more resistant to fatigue. Carbon (C), Chromium (Cr), Vanadium (V), Silicon (Si), Manganese (Mn), Phosphorus (P), Sulfur (S) or Copper (Cu) can then be added to this alloy. These different compositions will make it possible to have variants of these 3 classes.
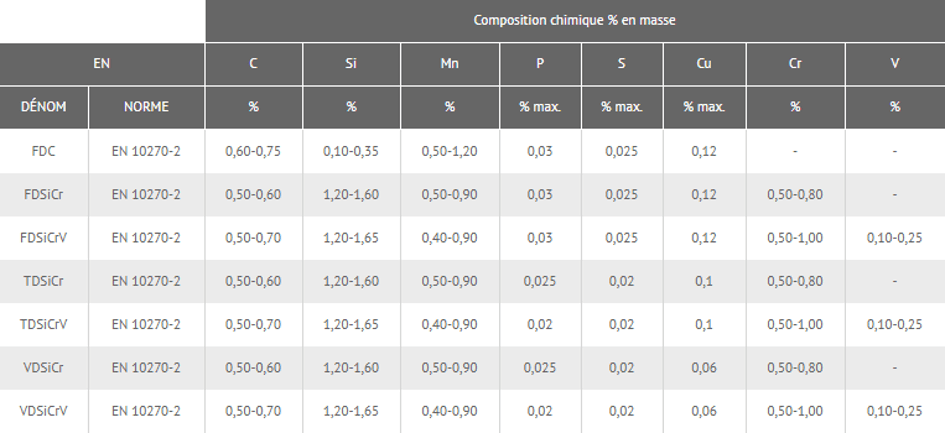
Application for a spring made from oil-hardened and tempered steel can be considered suitable for temperatures from -20 ° to + 170 ° C.
Stainless steels (EN 10270-3)
Stainless steel, commonly called INOX, is an iron-based alloy. It is made up of less than 1.2% Carbon and more than 10.5% Chromium. This chemical composition above 10.5% Chromium causes a surface layer called Chromium Oxide that makes it stainless.
There are 6 classes of stainless steels:
- 302 (X10CrNi18-8)
- 304 (X5CrNi18-10)
- 316 (X5CrNiMo17-12-2)
- 17.7 PH (Precipitation Hardenning) (X7CrNiAl17-7)
- 904L -> The suffix “L” means “Low Carbon”. (X1CrMoCu25-20-5)
- Duplex (X2CrNiMoN22-5-3)
These designations are the US designations except for the Duplex. Its name means there have two phases in its structure, ferrite and austenite.
For example for steel 302, the European designation is X10CrNi18-8 = 1.4310
The most commonly used stainless spring steel is INOX 302. What distinguishes these 6 classes of stainless steel is the chemical composition of the material. It affects their ability to resist heat or fatigue depending on whether it is static or dynamic work.
Prices also vary depending on the composition of the material. Stainless steel 304 is the cheapest while the most expensive are Duplex and 904L.
The modulus of elasticity and the modulus of torsion of stainless steel are generally lower than those of steels EN 10270-1 and EN 10270-2. Duplex steel is the material that provides the characteristics closest to the first two classes of steels with almost the same values for the two modules. A benefit to be confronted, however, with its much higher price.
Most of these spring materials can work between -200 °C up to 250 °C or even 300 °C for 17.7 PH stainless steel, 904L stainless steel and duplex.
The spring materials used for the realization are numerous. With this brief overview of the EN 10270 standard, you will thus know which ones are commonly used as well as some of the possible variations within each family. Note that more nuances exist and that any manufacturer of custom or specific springs is able to support the choice of the most judicious material.